Blasting without waste.
Imagine having a 1,000m2 (10,000 ft2) blasting project, and being able to blast it with virtually no abrasive to dispose of afterwards. Imagine creating only 500kg (1,000lb) of waste abrasive for the entire project. To most blasters this does not sound possible. Yet it is possible. There are contractors doing this on a daily basis. And they are saving a heap of money in waste disposal and abrasive costs.
Expendable abrasive comparison.
Firstly let’s take the same area and imagine we blast it the convention way with expendable abrasives.
First up we will blast with a heavy metal expendable slag. The consumption rate of slag would be approx. 40kg/m2 (7.6lb/ft2). So for 1,000m2 of blasted steel, we would end up with 40,000kg (88,000lb) of waste to dispose of.
Now instead of slag let’s assume it is blasted with expendable garnet sand. The consumption rate of this could be up to 12kg/m2. For that same area we would create 12,000kg (26,400lb) of waste. Bear in mind garnet sand is also a lot more expensive than slag abrasives. So the lower consumption does not necessarily mean it is cheaper.
In both instances we end up with huge amounts of waste abrasive that must be gotten rid of. No responsible contractor will just dump it anywhere. And most state and local Governments ban the dumping of this type of waste, except to designated toxic dumping grounds. So it must be disposed of properly, through a licensed waste disposal firm. Whenever you have to pay licensed waste disposal contractors to get rid of your crap they will charge you. Usually they charge big. In some places it is actually as, or more, expensive to dispose of the waste, as it is to buy the abrasive in the first place. Figure that.
So to recap this imaginary blasting project. We have had to pay for, and pay for the disposal of, 12,000 – 40,000kg of abrasives to blast an area 1,000m2 (10,000ft2). Regardless if it’s slag or garnet, kg or lb, this is a lot of abrasive to buy and dump.
The better way.
Fortunately there is a better way. For the same blasted area, a Blastrac Portable Enclosed Blaster would consume approx. 500kg of abrasive. To put this into perspective that is 1/24th to 1/80th of the amount of abrasive and waste. That alone is a huge saving.
Higher production and higher profits.
But that’s not the only advantage. Profits can be substantionally increased with very high blasting production rates. One operator with a Blastrac can blast, in the same time, 6 to 8 times the area of a blaster with a nozzle. Instead of 10m2 (100ft2) per hour your operator is producing 60m2 (600ft2). Most blasting contracts are based on a per square meter, or per square foot, rate. So blasting 6 times faster equates to producing 6 times the income, in the same time period. And at a fraction of the cost for abrasive and waste disposal.
Furthermore there is no need to erect scaffolds, curtains and tarpaulins. No need to protect surrounding areas from dust and flying abrasives.
One simple machine.
All this is achieved by using one simple blasting machine.
The Blastrac Portable Enclosed Blaster uses the blasting power and productivity of a turbine wheel shot blaster. The turbine is fitted into a mobile walk behind Blastrac. The operator merely points the Blastrac in the direction he wants to blast, presses the start button and walks along behind it. The Blastrac is self propelling. Once the Blastrac has completed its blast the operator turns it around, to point in the opposite direction, and starts off blasting again. As it is blasting, all abrasive and dust is contained and recycled within the enclosed head of the machine.
It is this continual recycling of the abrasive that results in such a small amount of waste being generated. In fact the rule of thumb consumption rate for blasting steel products is 0.5kg/m2 (0.22lb/ft2).
The high production rate is achieved due to the efficiency of the electric turbine throwing wheel. This method of propelling abrasive is at least 6 times more efficient, per kw or hp unit of power, than propelling abrasive with compressed air. When you throw 6 times the amount of abrasive, you blast 6 times as fast.
Note. As the abrasive used in a Blastrac machine is manufactured, and is not a waste by-product or scraped from a beach, it does cost more than expendable abrasives. But it does not cost much more. When compared to garnet the purchase price is maybe 2 or 3 times more. When compared to slag it is maybe 4 to 5 times the cost. But the new abrasive purchase price is only half the story. The other half, of course, is the disposal cost. Let’s assume the abrasive disposal cost is 50% of the initial abrasive purchase price. The total abrasive and disposal cost by using a Blastrac Portable Enclosed Blaster is still going to be 1/12 to 1/24th that of using expendable abrasives. So the abrasive cost may be more up front, but in the end it will save you money.
Blastrac applications?
So where can the Blastrac Portable Enclosed Blaster be used? The maximum productivity and benefits of this equipment can be achieved when blasting anything with large flat steel surfaces. The bigger and flatter the surface is, the more productive the equipment is. This equipment is not designed for blasting odd shaped bits and pieces or small items.
Ships.
Ships offer lots of areas that can be efficiently blasted with a Blastrac. The blasting is for the preparation of new steel before painting, or to remove an old coating before re painting. Ship deck, ship internals and ship sides. Car carrier decks that require recoating. Aircraft carriers require their runway coating to be replaced every few years. A Blastrac machine is the fastest and most cost effective way to do this.
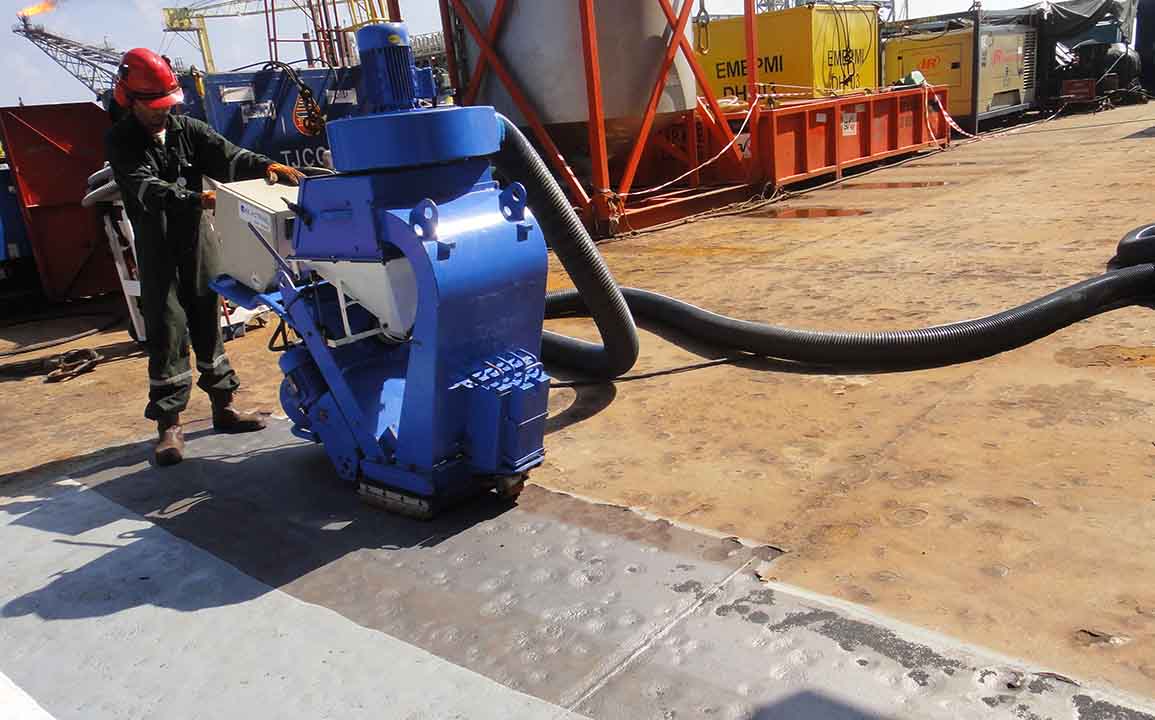
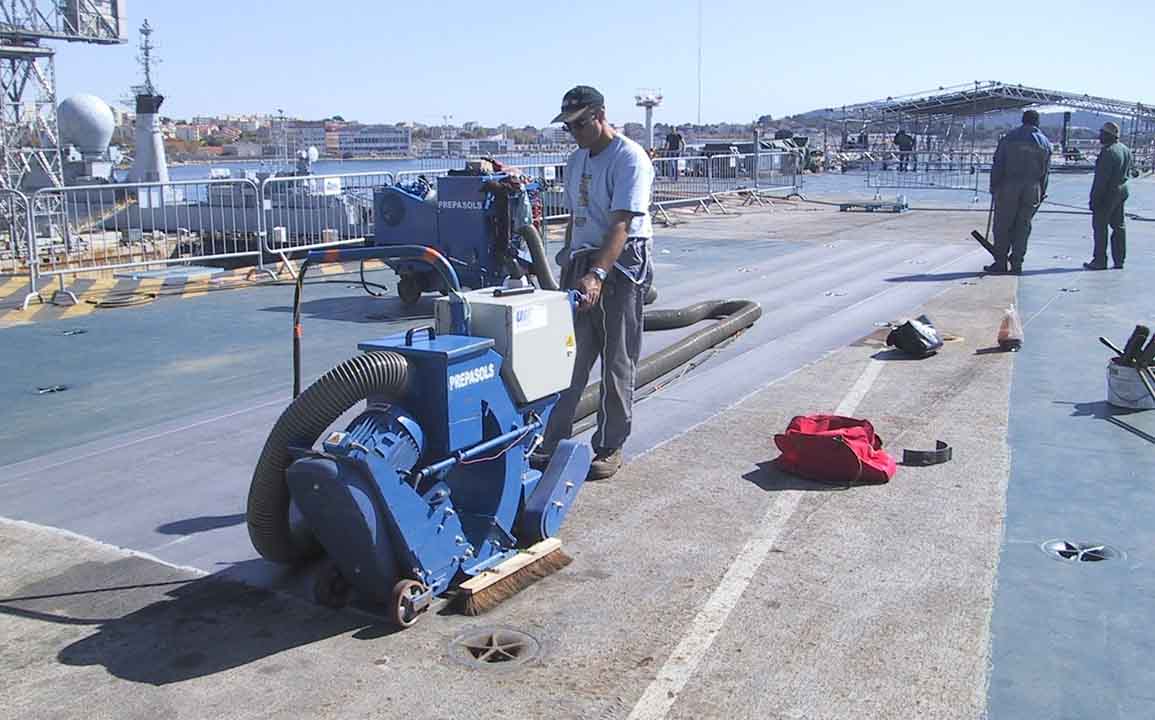
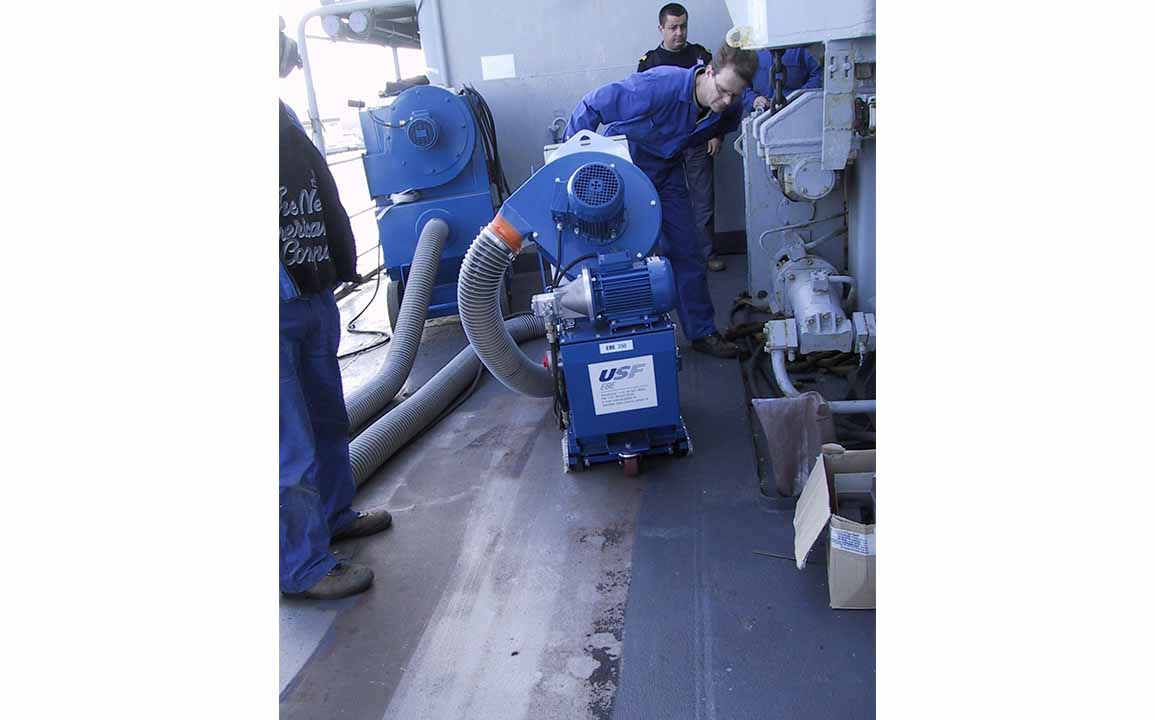
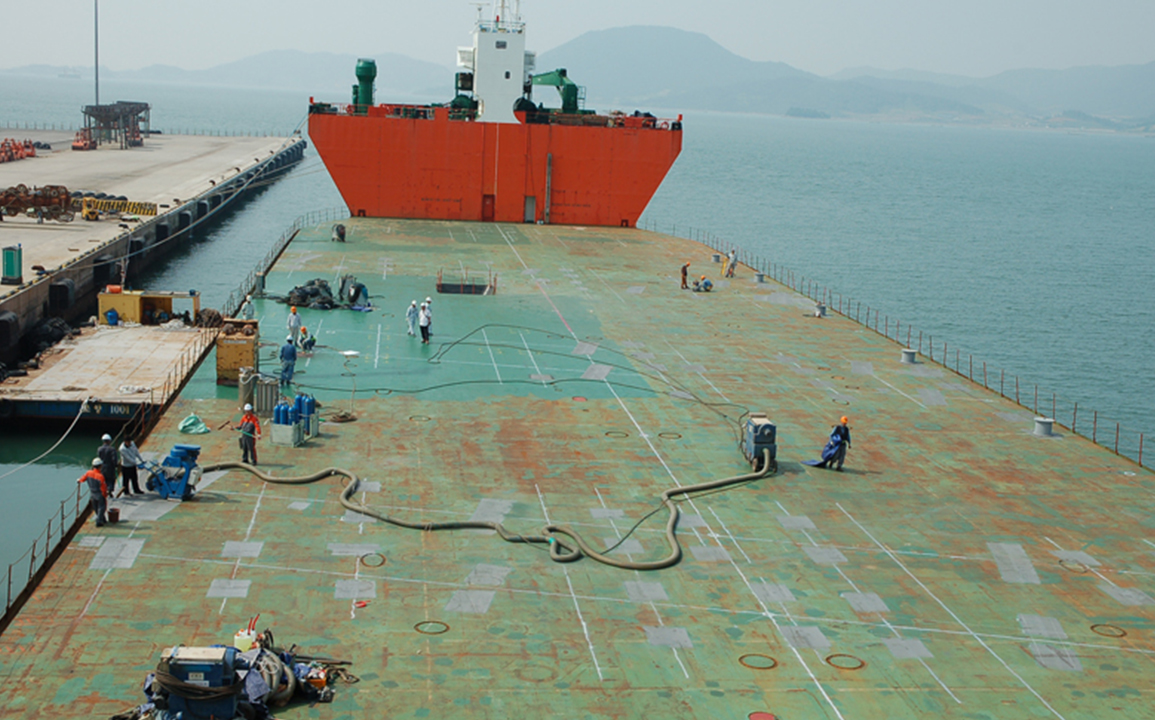
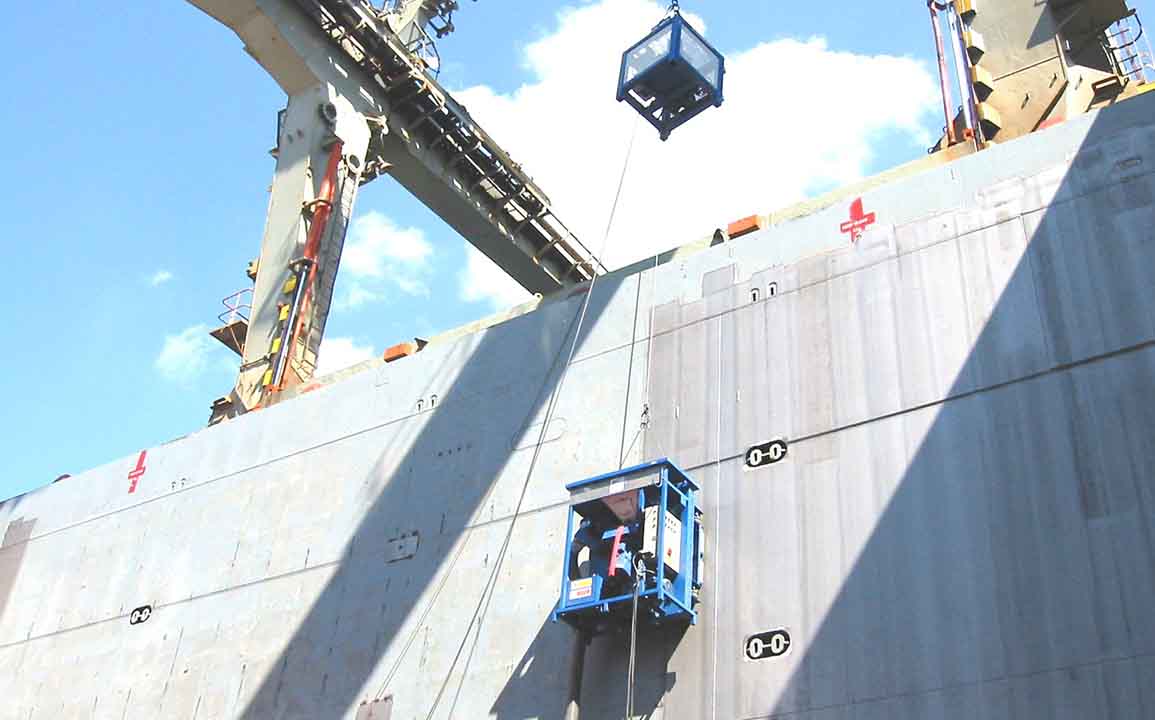
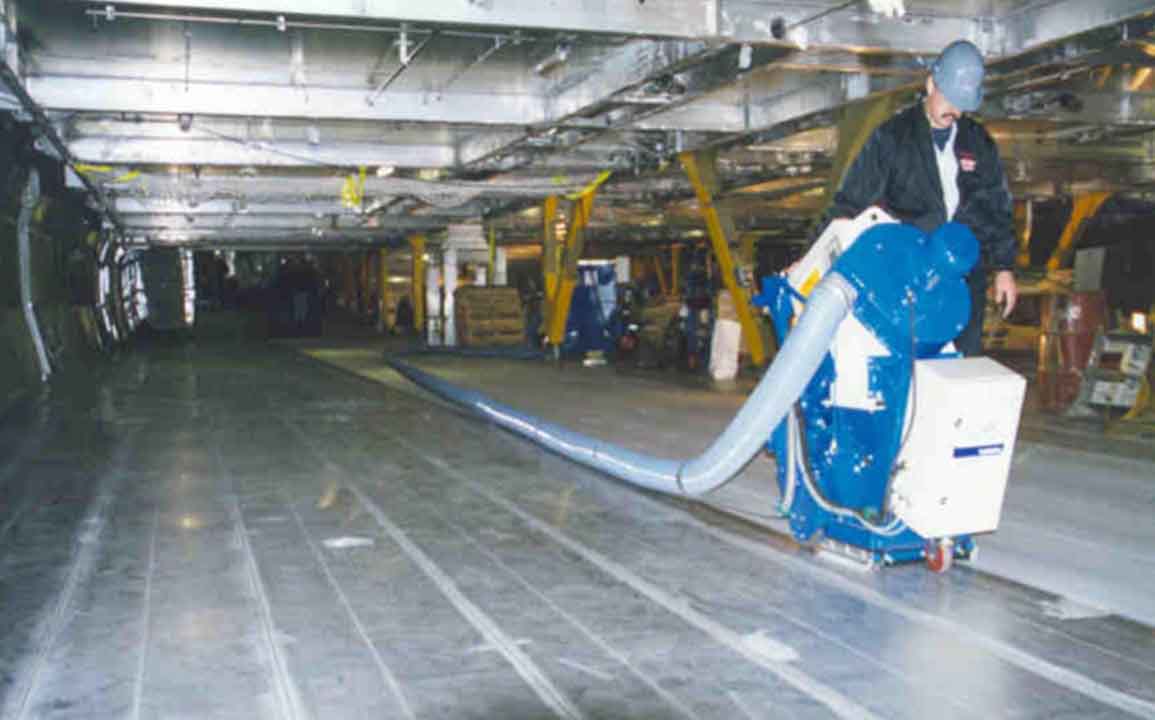
Ship repair.
Ship repair facilities use Blastrac vertical blasters, fitted to a travelling gantry, to remove coatings from ship side. There is even a special unit for blasting the underside of ships in a dry dock.
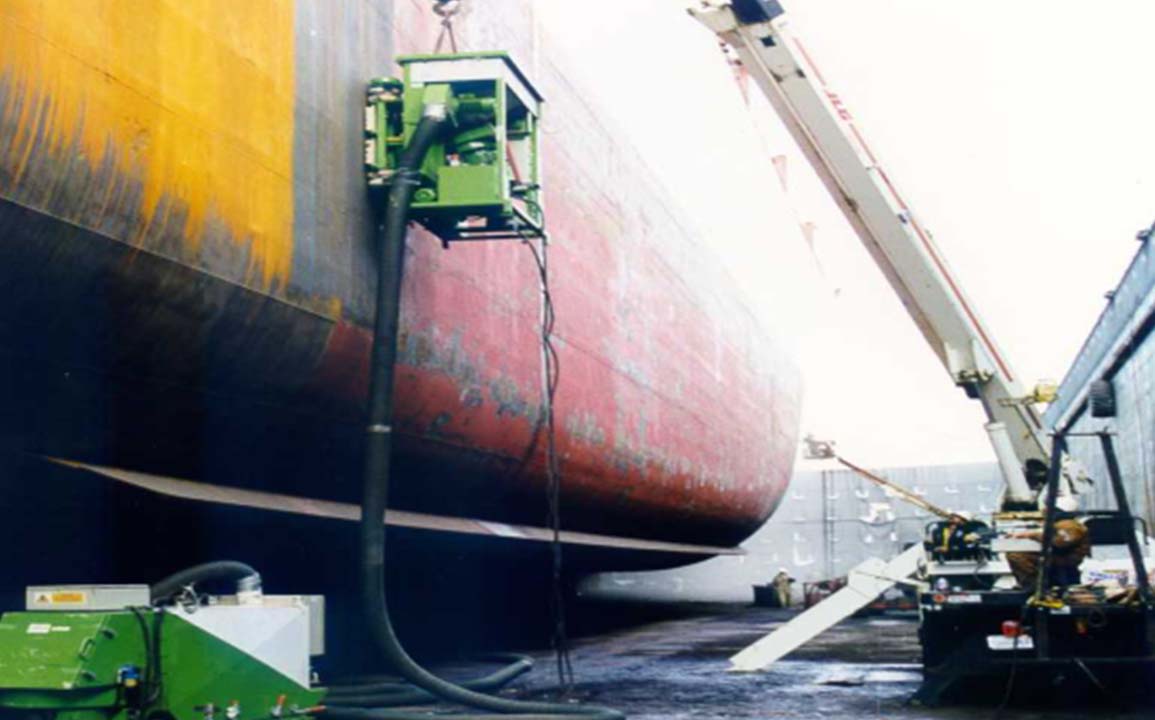
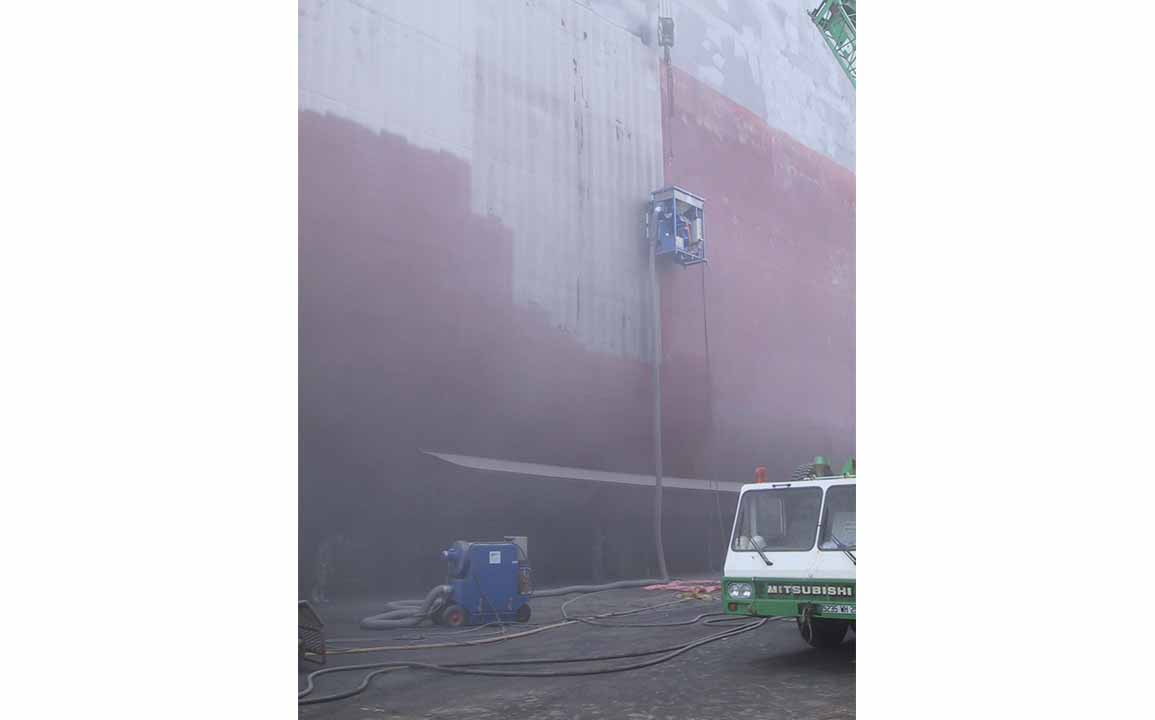
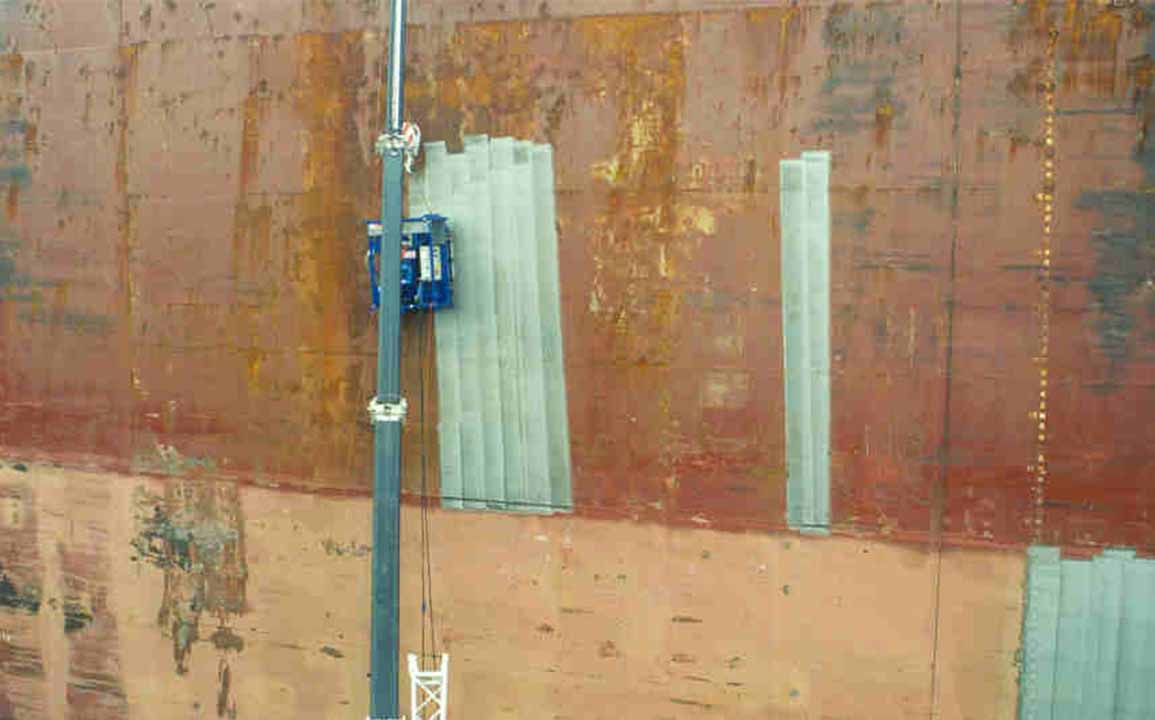
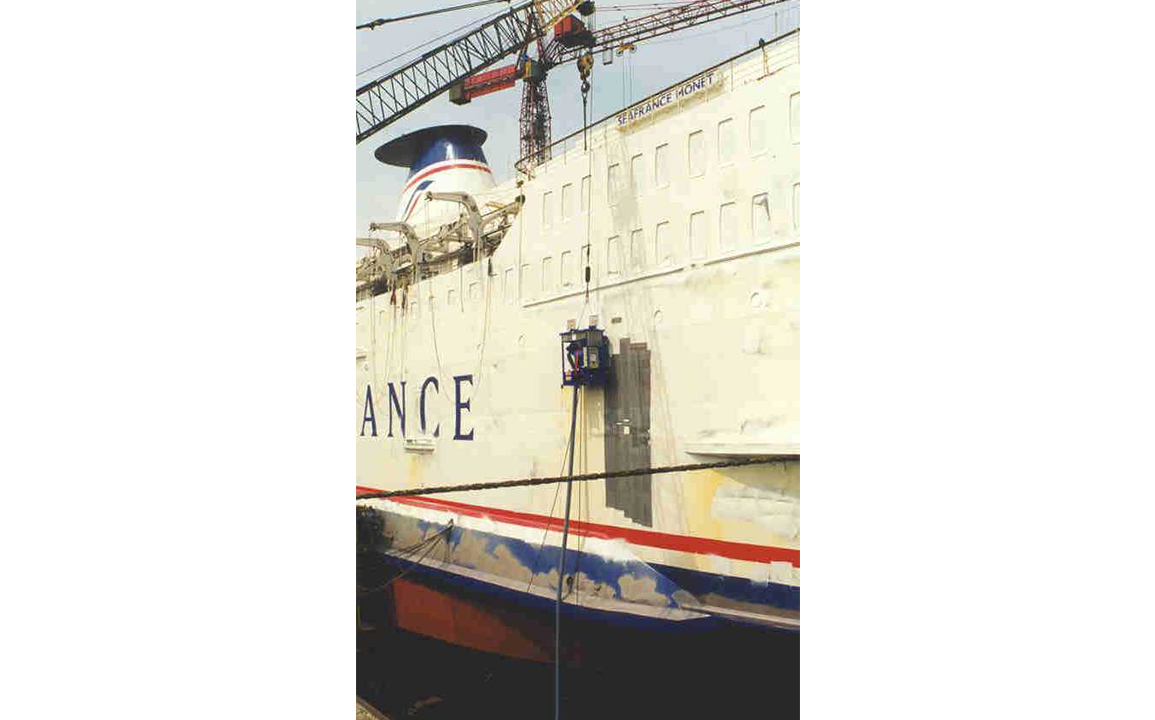
Oil storage tanks.
Oil storage tank facilities have huge areas of steel that require blasting. During construction of the tank the internal bottom requires full blasting before coating. Blastrac horizontal blasters are suitable for both the tank bottom and tops. Blastrac vertical blasters, suspended on wires ropes, crawl up and down the vertical walls of the tank and remove old coatings and leave a perfectly cleaned Sa2.5-Sa3 surface ready for recoating. There are also special versions of Blastrac horizontal blasters that are custom built to meet oil refinery strict safety requirements.
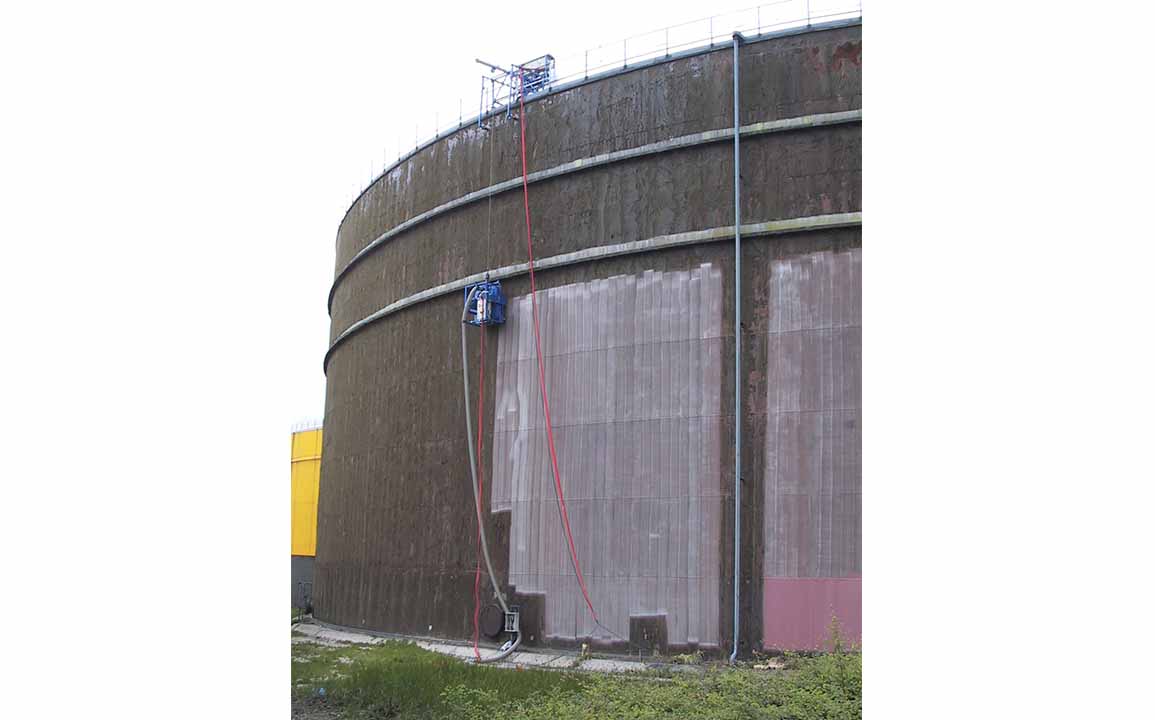
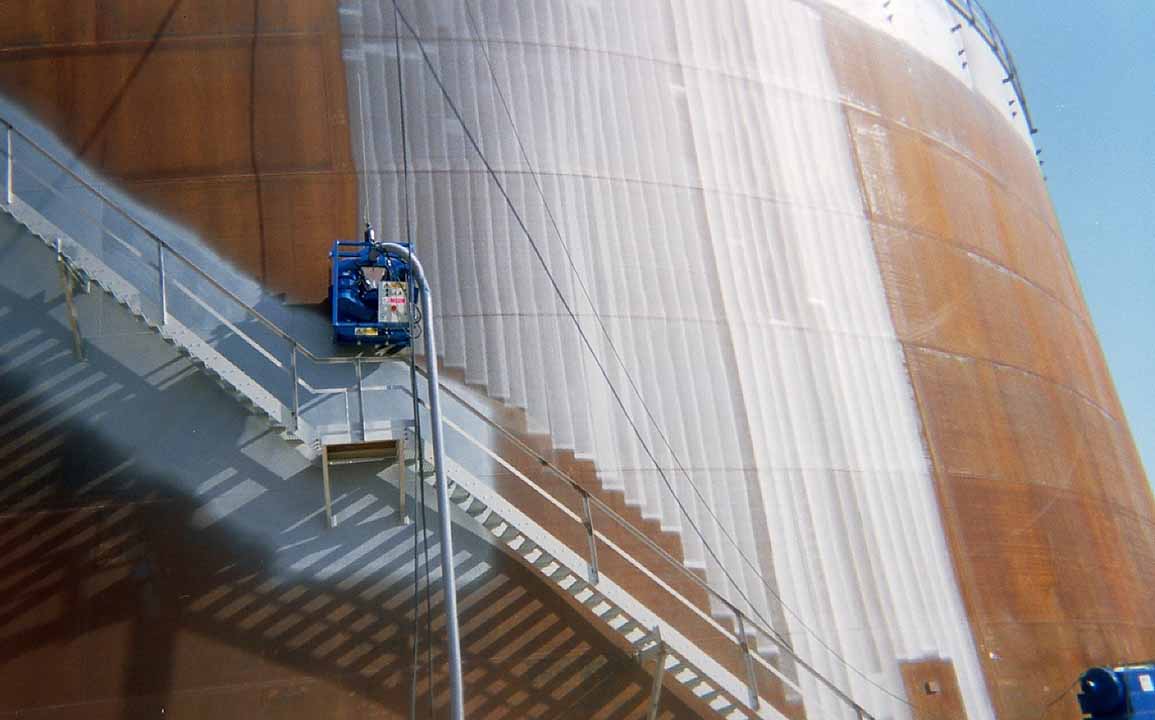
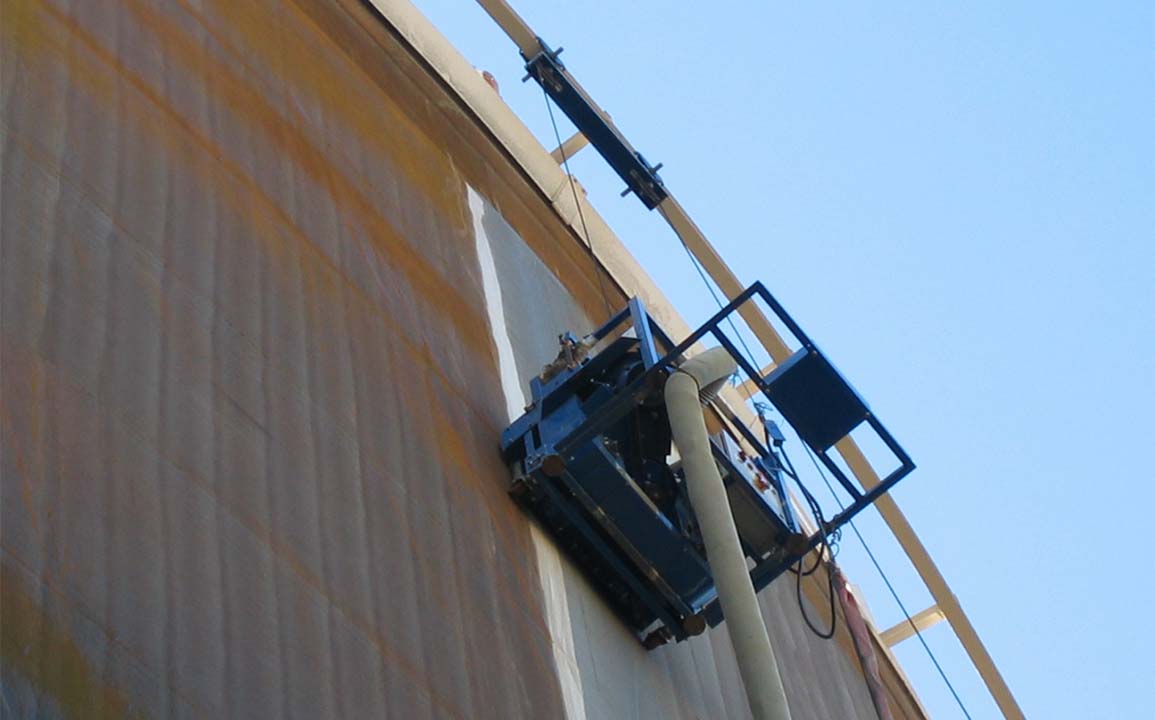
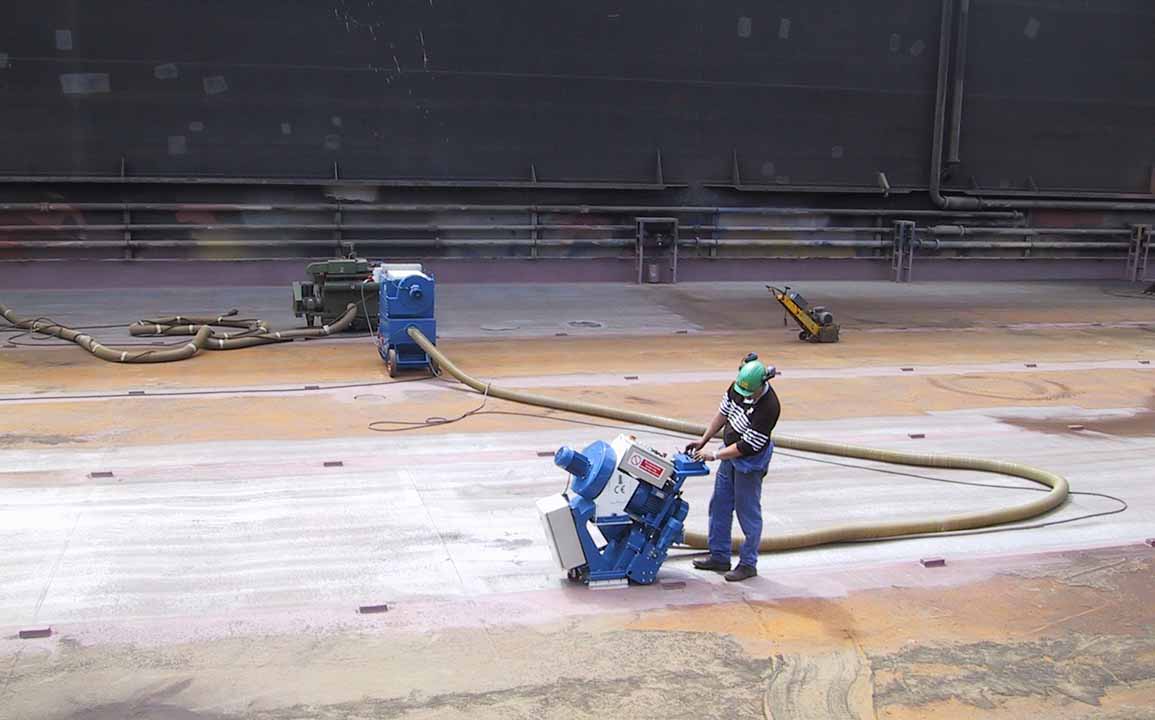
Offshore platforms.
Blastrac machines do not produce any pollution. This makes them especially suitable for work on offshore platforms. Helipads and decks of platforms require periodic recoating. When blasted with a Blastrac machine there is no pollution and, minimal abrasive to be transported to and from the platform.
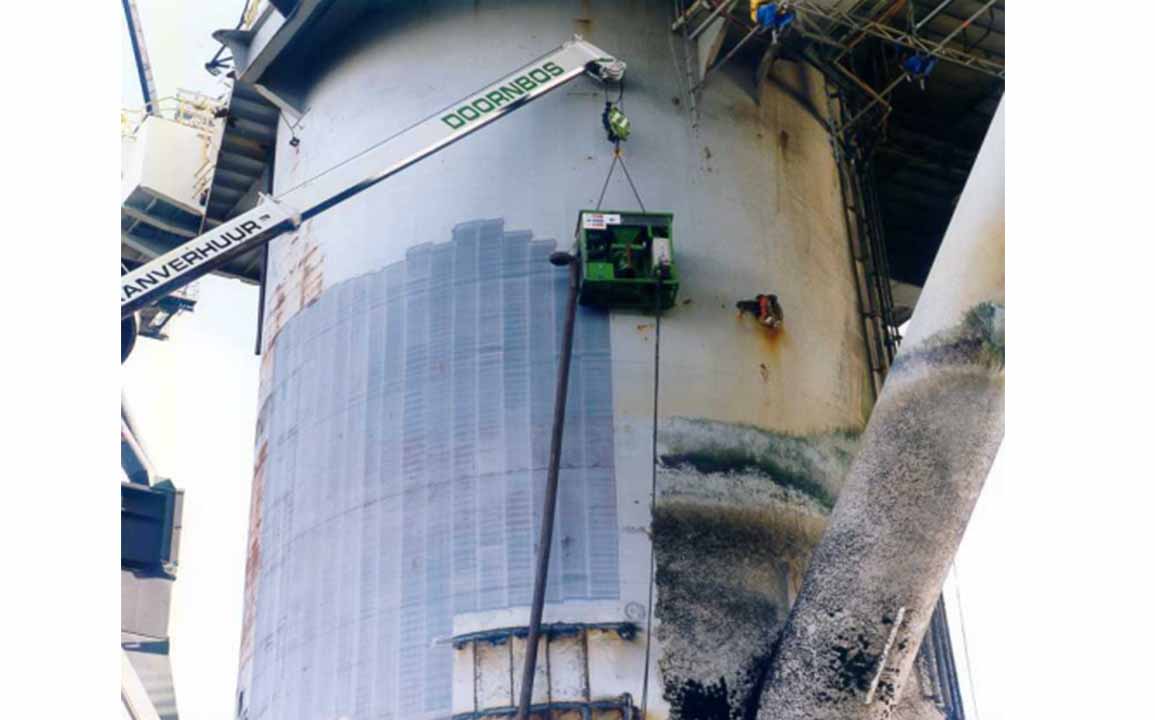

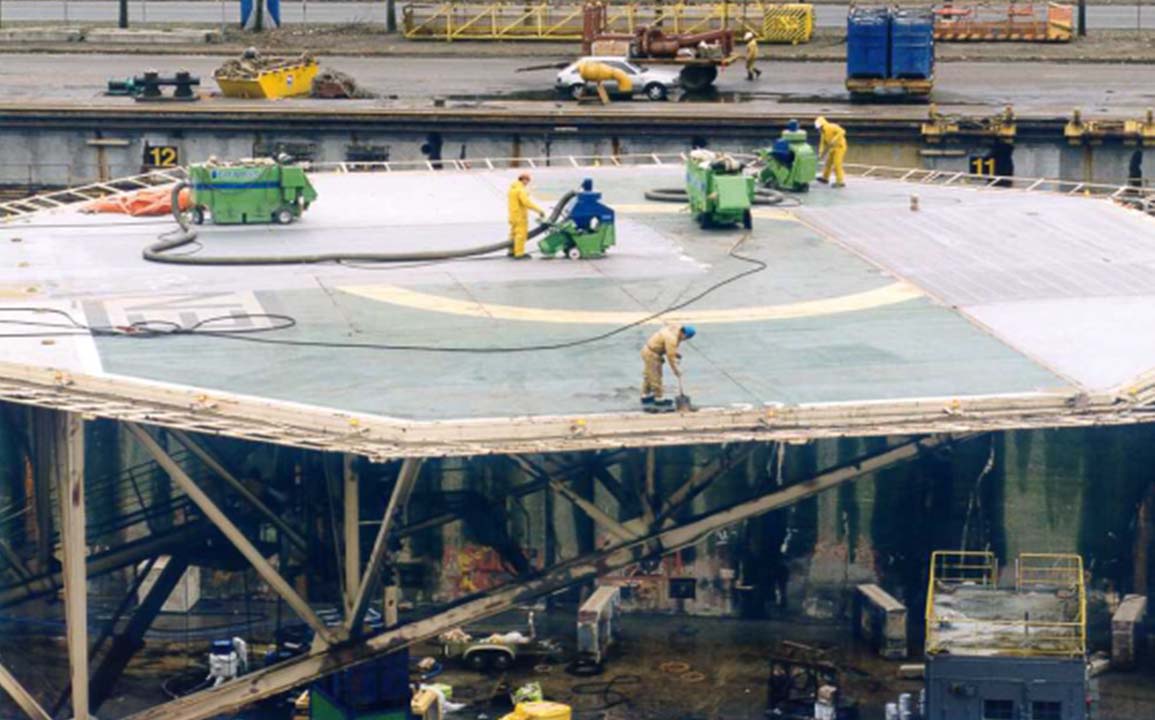
Steel plate.
Maybe you have a huge amount of steel plate to blast. The investment for a fixed turbine wheel shot blaster can be cost prohibitive for one project. Furthermore, this equipment is only suitable for permanent installations and is not suitable to move from site to site, project to project. A Blastrac blaster can be brought anywhere, anytime, no dismantling and re-erection required.The blasting of steel plate with a Blastrac is very easy. Simply layout the plates on a flat area and blast one side. One completed, turn over and blast the other side. If you have enough space you can even tack weld several plates together and blast all at one time.
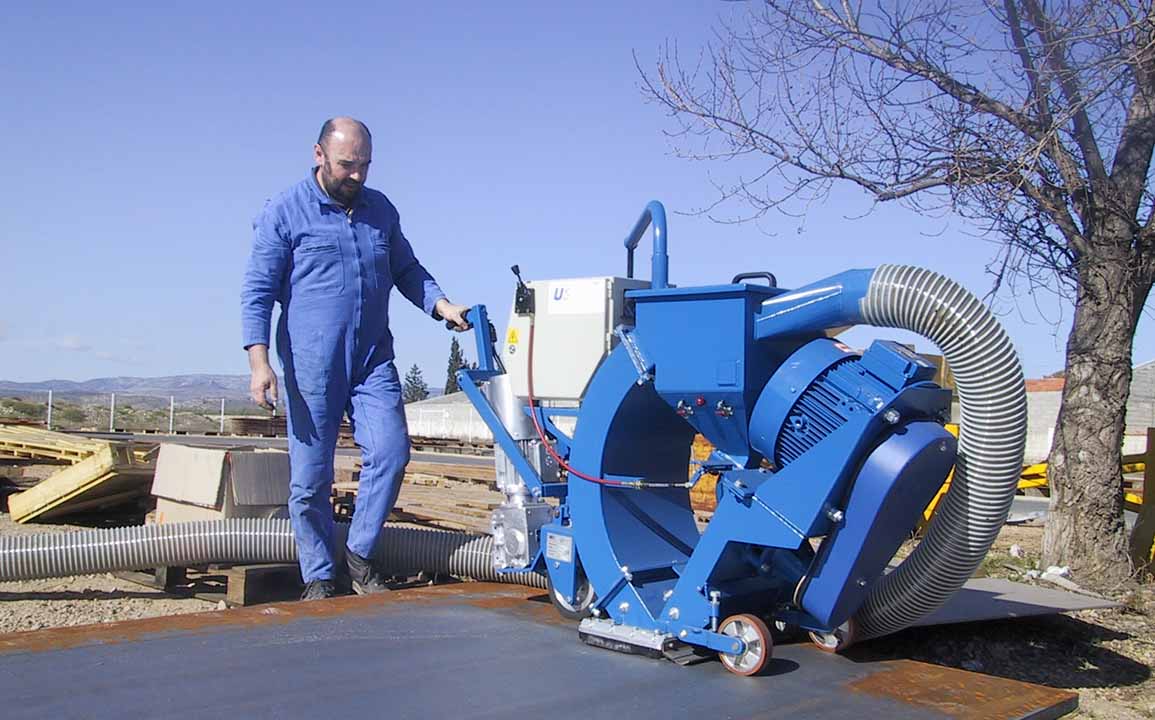
Steel pipes.
Pipes are a similar application to steel plates. For blasting lots of pipes the most effective equipment is a fixed turbine shot blaster. As the pipe has to travel through the blaster these machines require a space at least double the length of the pipe. So substantional space is required for feeding the pipes into, through and out of the blaster. Furthermore this type of equipment is designed for a certain range of pipe sizes. Pipes bigger than the machine is designed for cannot be blasted. Alternatively a Blastrac can be fixed to a forklift attachment. The pipe is rotated and the Blastrac slowly moved down the length of the pipe. No dust, no mess, no waste disposal. As the Blastrac travels the length of the pipe the Sa2.5 cleaned surface is revealed. The units can even be mounted inside the pipe to clean internals.
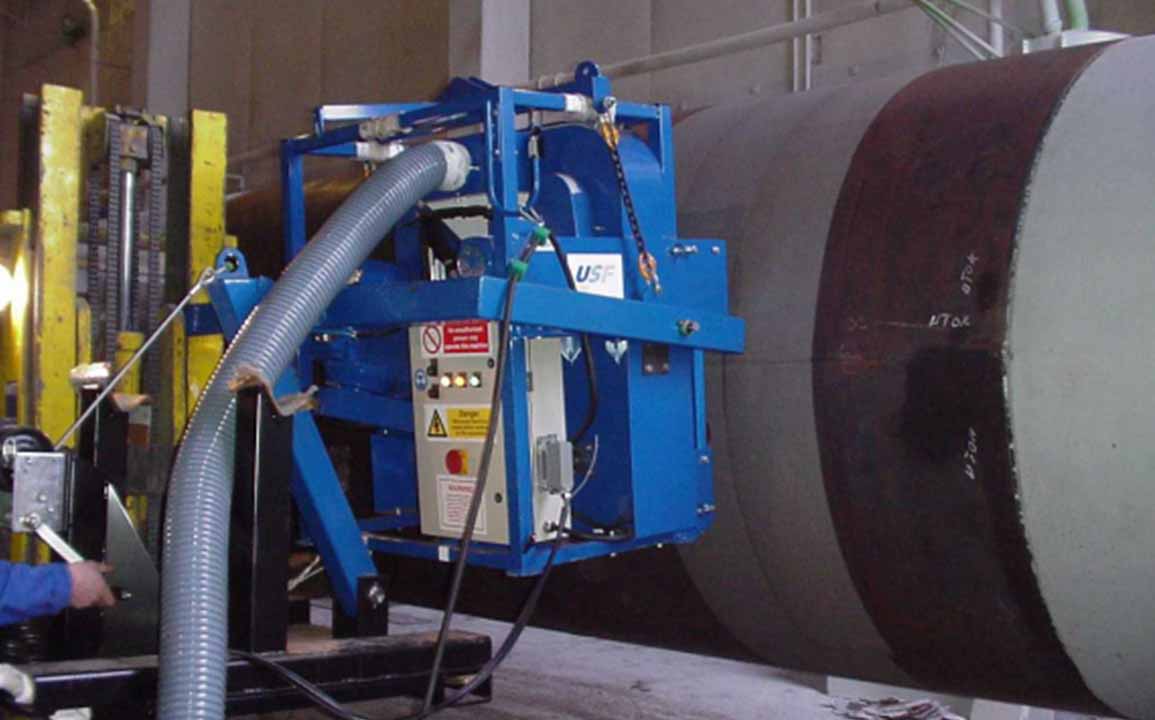
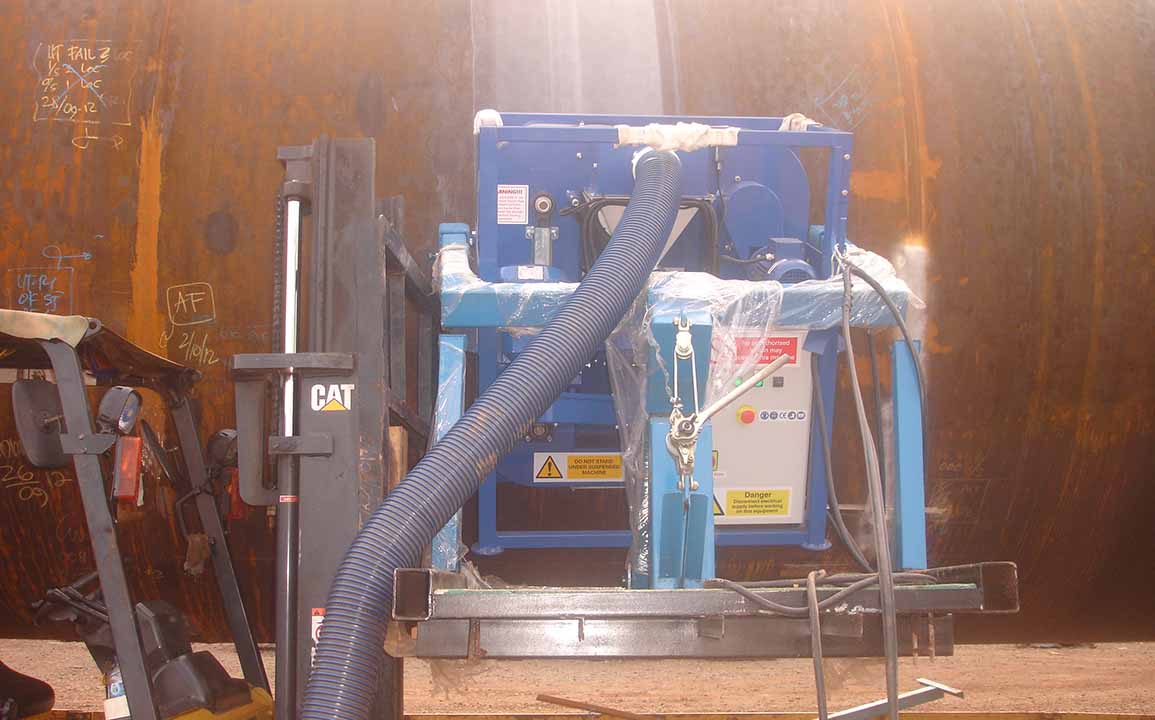
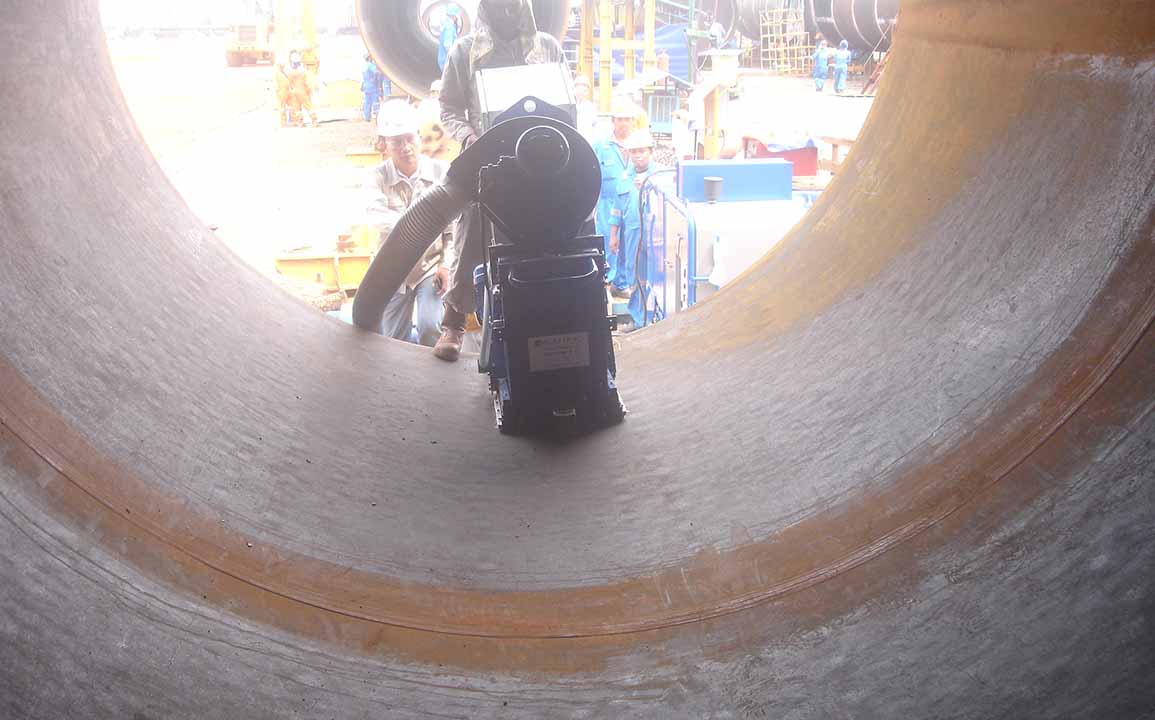
Steel bridges.
Bridge decks are frequently made of steel. This steel structure requires corrosion protection before being put into use. The steel plate is first blast cleaned and then coated with a protective coating. After coating the overlay of asphalt or concrete is applied. Due to the large size of bridges, this application has huge areas to blast. The purpose built Blastrac 2-48DS shot blaster is fitted with two blasting wheels to provide the widest blasting pattern, 1,200mm. Due to the size of the areas involved the 2-48DS is also available as a ride on or truck mounted unit.
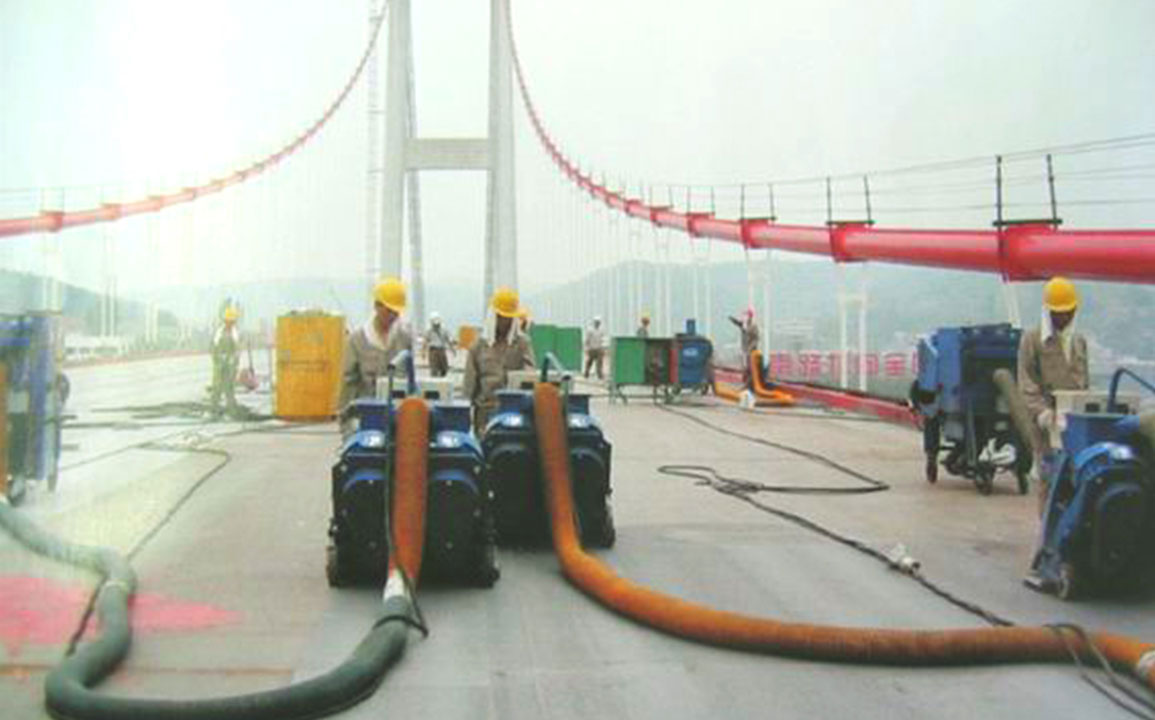
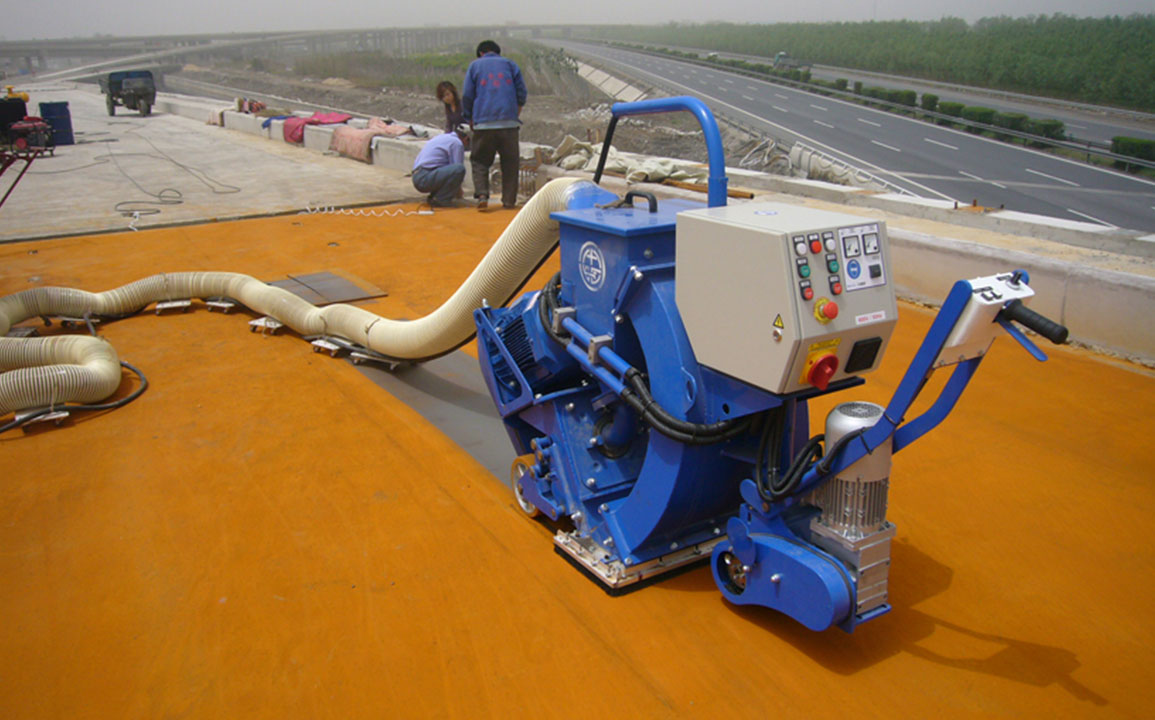

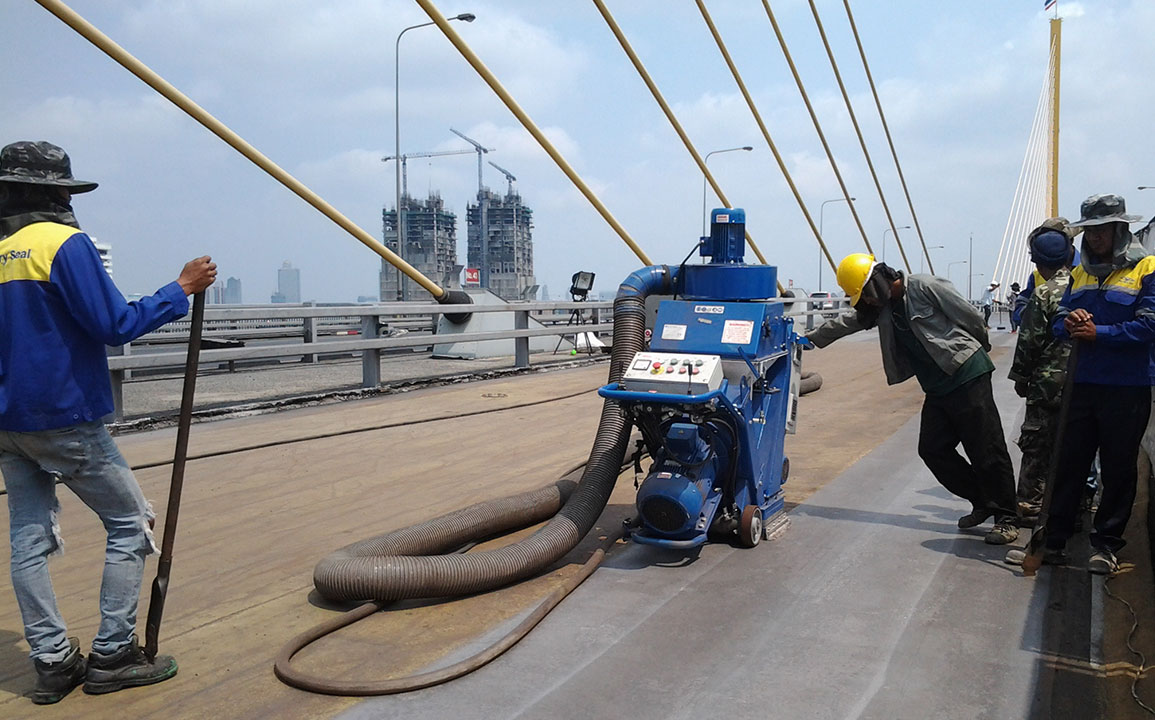
The best way to blast.
As you can see there are many applications that can use Blastrac equipment. In all the instances above the contractor will save time and expense to complete the project. Faster blasting times, lower abrasive costs, lower clean up costs and lower disposal costs. If you have large steel areas to blast, and want to earn more money doing it, this is the best way to blast.
With a bit of engineering ingenuity, and our years of practical Blastrac blasting experience, we will advise and help you set up a perfect blasting rig for your application.